The promise of shape memory materials (SMMs) is, in many ways, an engineer’s dream: materials capable of undergoing large, reversible deformations and returning to a predefined shape when triggered by external stimuli such as heat, light, pressure or electricity. This shape memory effect has opened the door to countless design possibilities, from deployable aerospace structures to self-fitting biomedical devices.
While shape memory alloys (SMAs), such as nickel–titanium, have long been the most widely used SMMs due to their high actuation force and reliability, growing interest in new materials and possibilities has led to growing R&D investment in shape memory polymers (SMPs).
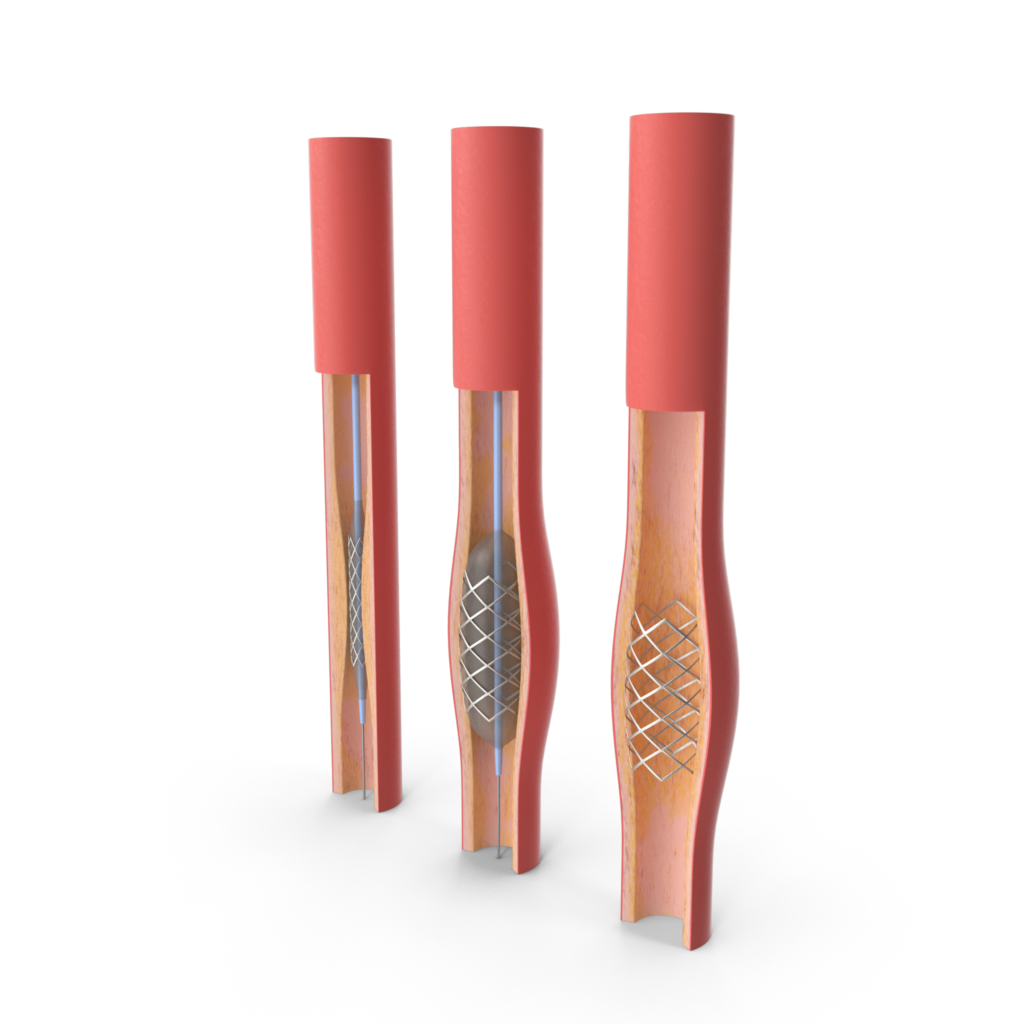
Figure 1. The most popular memory shape material is nitinol, a nickel titanium alloy used for vascular stents among many other uses, for their ability to withstand external compression forces.
One of the most promising evolutions in the field of shape memory materials is the development of shape memory polymer composites (SMPCs). By reinforcing SMPs with fibers, nanoparticles, or other functional fillers, researchers are expanding their mechanical strength, functionality, and environmental resistance—without sacrificing the inherent advantages of polymers, such as low weight and design flexibility.
These composites can simultaneously achieve high actuation strain and improved stiffness, conductivity, or thermal properties, opening the door to high-performance applications. Among the different families of shape memory polymers, epoxy-based SMPs (SMEPs) are attracting particular attention due to their excellent mechanical performance, thermal stability, and chemical resistance.
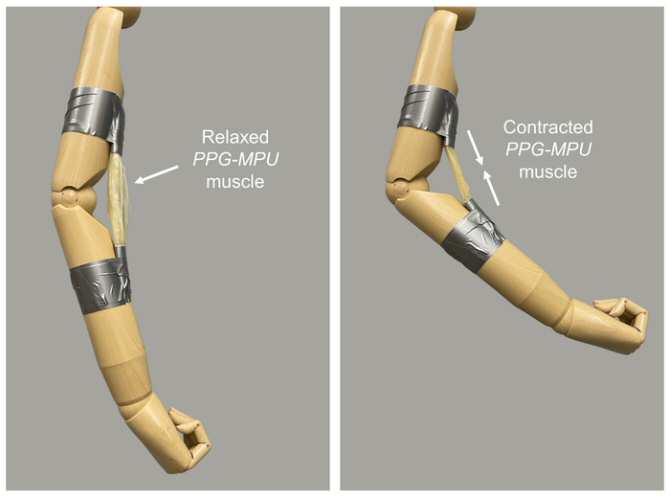
Figure 2. An artificial muscle comprised of prestrained films of PPG-MPU (3.8 g) actuates a full-size mannequin arm (0.6 kg) upon heating. Photo Credit: ACS Central Science 2021, DOI: 10.1021/acscentsci.1c00829
Epoxies are already well-known in structural and high-performance applications, and their transition into the field of smart materials is a natural evolution. SMEPs combine the adaptability of SMPs with the structural integrity of epoxy networks. Their highly crosslinked structure allows for precise programming of the shape memory behavior, while offering superior dimensional stability compared to thermoplastics. Current research is focusing on tuning their properties through tailored curing systems, molecular design, and hybrid formulations—resulting in systems with faster recovery, multi-shape capabilities, and even self-healing features.
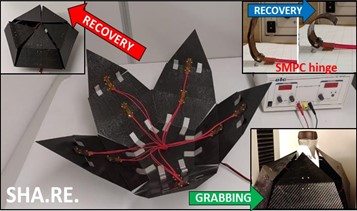
Figure 3. Smart grabbing device with shape memory polymer composites (SMPC) activated through external heating system. Photo Credit: Department of Industrial Engineering of the University of Rome Tor Vergata.
There is no doubt that shape memory polymers and their composites will see increasing real-world applications in the future, opening up a new range of possibilities for smart materials.
Stay tuned!