In the world of advanced composites, few materials have sparked as much curiosity—and as much misconception—as forged carbon fiber. Often associated with luxury design and aggressive aesthetics, its marbled appearance has become a symbol of exclusivity. But behind the surface, forged carbon is proving to be a material with legitimate structural potential—especially when applied with the right engineering criteria.
This article explores what forged carbon is, where it excels, where it doesn’t, and how it fits into the future of performance-oriented composite engineering.
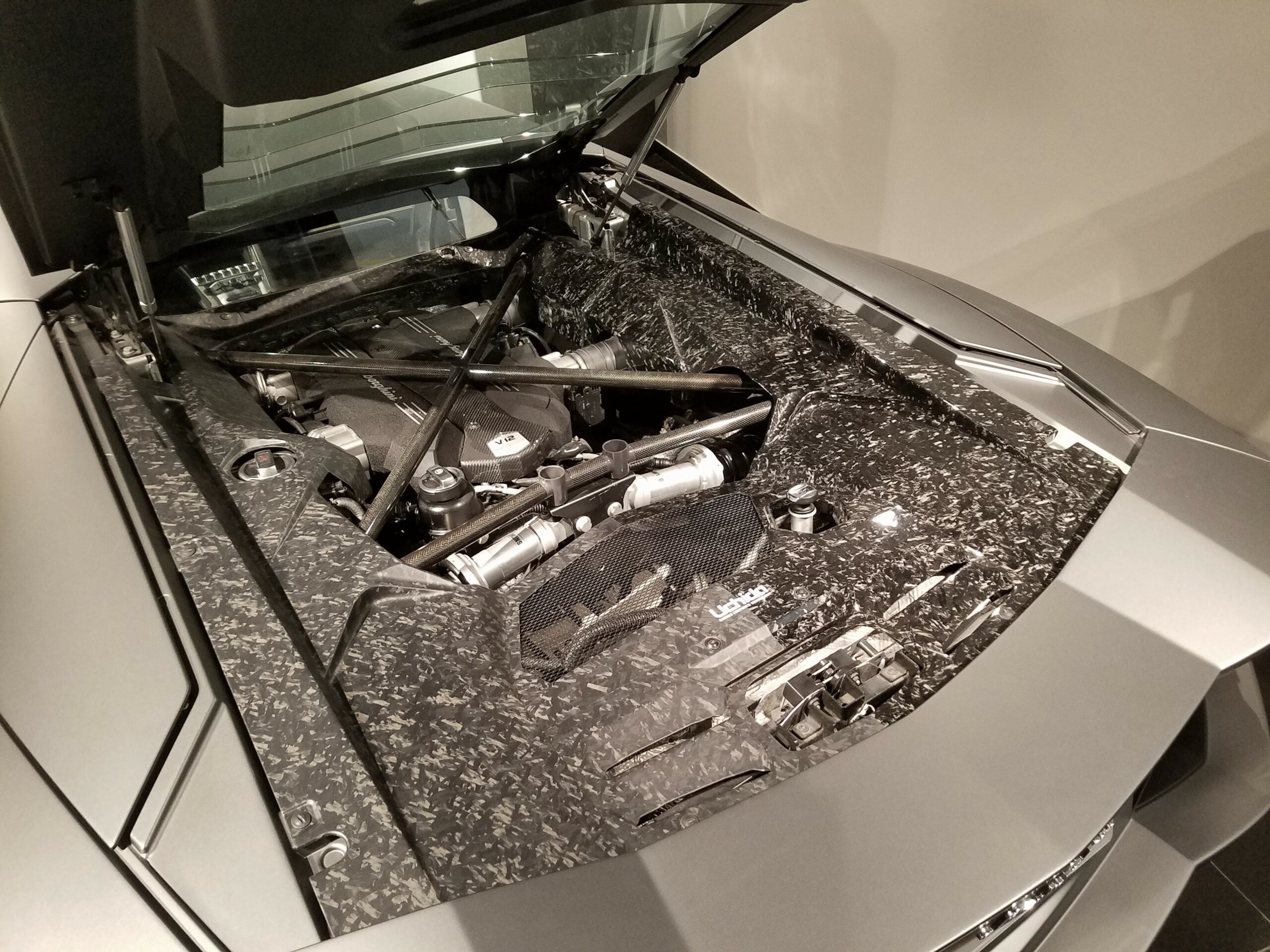
Forged Composite on prototype engine bay cover. Bw570, CC BY-SA 4.0
What is forged carbon—really?
Forged carbon, also known as forged composite, is made by compression moulding short, randomly oriented carbon fibers with resin. Unlike traditional prepregs or woven fabrics, forged carbon uses chopped fiber bundles that are distributed and compacted into complex shapes under high pressure and temperature.
This method enables geometries that would be unfeasible with continuous fibers. It also results in a unique, repeatable visual pattern—an attribute that has captured the attention of the luxury automotive and design sectors.
Forged carbon vs. continuous traditional carbon fiber: key differences
Understanding what forged carbon can and can’t do begins with comparing it to traditional continuous fiber composites.
- Continuous fiber composites offer maximum directional stiffness and strength. Fibers can be precisely oriented to match expected loads, achieving very high mechanical performance. However, these materials are less suitable for highly complex geometries.
- Forged carbon, by contrast, sacrifices directional performance in exchange for design flexibility and good isotropic behavior. Its random fiber orientation limits peak strength, but makes it more adaptable to multi-axial loads and unconventional shapes.
Performance matters: what the data shows
In a tests published by Easy Composites using their forged carbon fiber kit, the material demonstrated a flexural modulus of 35.5 GPa, a tensile strength of 192 MPa, and a density of 1.5 g/cm³. These properties were measured using real-world specimens manufactured without autoclave, simulating accessible fabrication conditions.
Compared to 6082-T6 aluminum, forged carbon showed a significantly higher strength-to-weight ratio in bending tests. While aluminum displayed higher modulus, forged carbon resisted nearly double the load before failure in three-point flexural testing (220 kg vs. 120 kg). Its lower density—about 44% less than aluminum—means forged carbon can offer superior mechanical efficiency in specific applications.
It’s worth noting that the fiber orientation in forged carbon is random, resulting in near-isotropic mechanical behaviour, which can be advantageous in components subjected to multi-directional loads. However, consistency and directional performance remain below what can be achieved with continuous fiber laminates cured under controlled conditions.
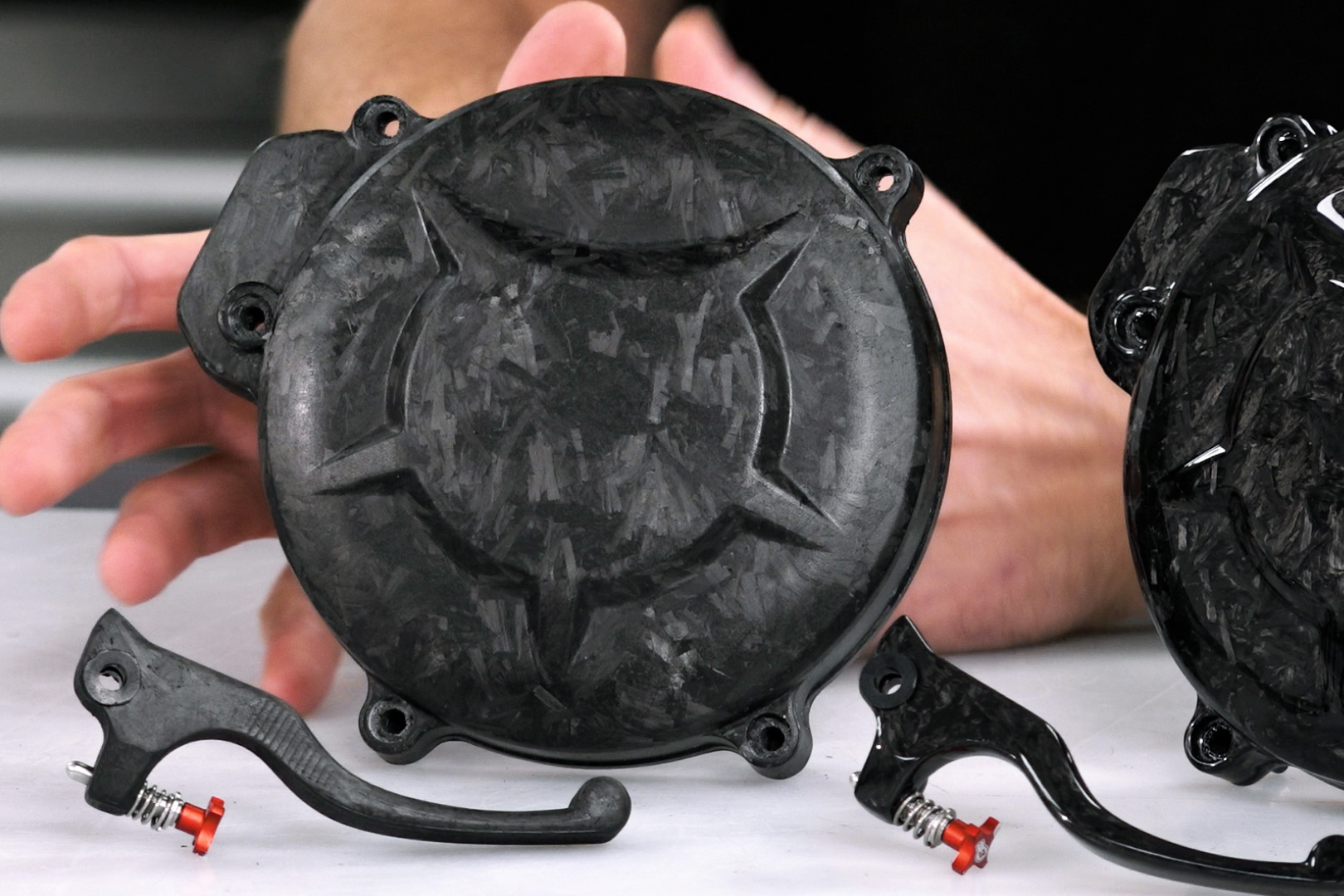
A clutch cover and a brake lever made of forged carbon by Easy Composites
Where forged carbon excels—and where it doesn’t
Forged carbon is particularly well-suited for:
- Complex-shaped parts with variable thickness, recesses or non-developable surfaces.
- Luxury interiors or visible parts, where the aesthetic of forged carbon is desired.
However, it is not recommended for:
- Load-critical structural parts, like monocoques, suspension links or roll structures.
- Applications under defined unidirectional stress, where continuous fiber composites are clearly superior.
- Contexts with minimal mechanical tolerance, as its fiber randomness introduces moderate variability.
A material with a future
Forged carbon is not a replacement for continuous fiber composites—it’s a complement. Its aesthetic-mechanical balance, ability to integrate recycled carbon fibers, and growing market presence make it a valuable asset in the portfolio of any advanced composite strategy.
From hypercars to high-end consumer electronics, forged carbon is opening a space where performance engineering meets expressive design. And as always, when used with criteria and control, it delivers much more than appearance—it delivers results.